Sustainable packaging is revolutionizing the appearance and transportation of goods. Thanks to modern technologies, packaging solutions are no longer just focused on aesthetics; they are made from eco-friendly materials that significantly reduce environmental impacts throughout their entire lifecycle. These packaging solutions not only aim to minimize waste but also ensure that products arrive safely and efficiently to users, all while utilizing the least amount of resources possible.
However, in Hungary, the widespread adoption of biodegradable packaging is still awaited. In this context, we sought insight from Viktor Rydzewski, the managing owner of our partner company CELLUX PACK Ltd., and asked him several questions about sustainable and biodegradable packaging. We were particularly interested in what innovations are currently present in the market.
- Do you currently offer biodegradable or recyclable packaging solutions? What are they?
“Our range includes biodegradable and recyclable packaging materials. For sealing boxes, we offer our partners paper and bio-based, plant starch-based compostable adhesive tapes. Among our recyclable materials, we have products made of paper as well as plastics, but the recycling of plastics is limited depending on the raw materials.” - What feedback do you receive from customers regarding eco-friendly packaging?
“We receive a lot of interest in these materials, which shows that while they are open to the use of environmentally friendly technologies, unfortunately, due to the currently high prices, our partners typically choose traditional packaging materials.” - What plans or developments are underway regarding eco-friendly packaging?
“Thanks to our close cooperation with our shipping partners, we receive information about new developments continuously. One such development is biodegradable stretch film, which is an environmentally friendly packaging material; it does not break down into micro-sized plastic fragments, but rather into a truly biodegradable, compostable material.” - What challenges do you encounter in the development of biodegradable/recyclable packaging?
“I believe that the development of biodegradable materials is heading in a positive direction. The industry is becoming capable of producing higher quality raw materials; however, the challenge lies in durability. I think there is still room for improvement.” - How do you see the market demand for these products in Hungary?
“Of course, everyone wants to be more environmentally conscious, but I see that not every company can afford it. This is due to the significant price difference between traditional and biodegradable packaging materials, making it so that domestic businesses cannot or can only partially incorporate it into the prices of their final products.” - Are there standards or certifications that these biodegradable packaging solutions must meet?
“Currently, I’m not aware of any ongoing regulations, laws, or directives. There is no certification for biodegradable materials, but compostability must comply with certain criteria and rules.” - How does EU plastic regulation impact your company’s strategy?
“We continuously monitor all regulations and standards because our company is fully committed to replacing all environmentally harmful products, not just in packaging but also in logistics. Therefore, our strategy remains unchanged, as our openness allows us to switch from one product to another as soon as the opportunity arises. In the packaging industry, the transition to eco-friendly products is slow but clearly shows a direction; however, it is certain that European manufacturers are at a significant disadvantage compared to manufacturers outside the EU. This may be because there are much stricter expectations and regulations in the EU that manufacturers must comply with.” - What collaborations do you have with research institutions or other companies in the field of sustainable packaging?
“Our company is consistently seeking opportunities to work with suppliers who are making continuous efforts in the market for innovative, eco-friendly, and affordable packaging materials.” - How much more expensive is the production of biodegradable/recyclable packaging compared to traditional options?
“Recyclable materials may not be that expensive, but unfortunately, biodegradable materials are available at 3-4 times the price compared to traditional ones.” - What innovations do you see as promising for the future in this area?
“The use of stretch film and adhesive tape is significant in Hungary, and I believe changes are expected in this area. While it is not possible to completely replace stretch film, the quantity used can be significantly reduced. Thinner and much stronger films are gradually gaining ground in our country, but this will take some time. It is certain that, in the future, alternative solutions will emerge, and we strive to make this a reality in the near future at an affordable price. Henkel Magyarország Kft., a subsidiary of Henkel AG in Hungary, is among the world’s leaders in adhesive technology. They present developments year after year, such as the application of slip-resistant materials in load formation. They have made significant contributions in the field of environmentally friendly, carbon-negative adhesives aimed at replacing box-sealing tapes. Adhesives that have OÉTI or FDA certifications (a significant portion of their adhesives holds one of these certifications) are extremely promising for the future because these adhesives are not only eco-friendly but also non-harmful to human health.” - How can the separation of biodegradable and non-biodegradable materials be handled during production?
“Stretch films or shrink wraps can be easily collected separately, and their recycling is feasible. Plastics that are incorporated into packaging are difficult or impossible to collect separately. An example of this is box-sealing adhesive tape, and Henkel Magyarország Kft. provides excellent solutions for this problem with their industrial adhesives.” - What steps are you taking to reduce your own ecological footprint during production?
“We are continuously developing our company; thanks to our investments in cutting and rewinding machines, we no longer procure and sell finished products, but instead, we handle raw materials ourselves, significantly reducing the amount of waste generated by our operations. In addition, we collect paper and plastic packaging materials separately and deliver them to recycling points.” - Is there government or EU support available for eco-friendly developments?
“It is essential to consider the most important fact that finished and packaged products must reach the customers at their usage locations without damage. There are alternative solutions that can help reduce the amount of packaging material used. This can happen through optimization, but there are also possibilities to replace the currently used packaging with more modern, thinner, and more efficient materials. When procuring packaging materials, the length, width, and thickness of the materials used must be taken into account. Here are a few examples: The length and width of manually used box-sealing tapes available in Hungary show a wide range. If the length of the adhesive tapes were significantly greater than it is currently, the transportation and storage costs would be lower, and the amount of waste generated by users would significantly decrease. Securing loads on pallets is also an area where the amount of stretch film used can be significantly reduced. High-quality, thin films with high stretchability require less material than traditional thicker films. Pre-stretched films and roll-less films can also provide good solutions for reducing the amount of packaging material used.
Naturally, each company shapes the packaging of its products independently and may not be aware of alternative solutions. For our partners who require this, we try to assist in selecting the appropriate adhesive or packaging material. We have the option to manufacture customized products tailored to specific companies and application areas, though these developments take longer. With these solutions, we do not eliminate waste derived from packaging or the application of polluting materials in terms of our environment, but we can reduce the overall amount.”
- Is it possible to apply for government or EU funding for environmentally friendly developments?
“There are subsidies for the recycling of plastics and the production of environmentally friendly packaging materials.”
- How do you see the future of biodegradable/recyclable packaging in the industry?
“This is a slow process, and it will only accelerate when it becomes advantageous for companies to use these materials. Naturally, this is also our responsibility, as without appropriate information, users cannot make responsible decisions. I am very hopeful about the widespread adoption of these materials.” - Do you usually inform your customers about eco-friendly packaging? What do you typically do in this case?
“We provide continuous information to our partners about new, efficient, and environmentally friendly products. We offer engineers and sample materials for free, and we present the developments on their own premises. These demonstrations are usually quite successful.”
Here’s an interesting fact that Viktor shared with us:
“Polyethylene can typically only be recycled once, while polyester can be recycled multiple times. Polyethylene is often mixed with additives that help it break down into micro-sized particles, but unfortunately, it can remain in the environment for 200-400 years. PLA (polylactic acid) can be 100% biodegradable and compostable, provided the right conditions are met. PLA is made from plant starch, but it must also be polymerized, which causes it to lose some of its natural qualities. In my opinion, this is the best alternative by far, but its production costs are quite high. It would be a huge breakthrough if chemists could develop a truly compostable material that works under all conditions.
Producing PLA requires corn, potatoes, or sugarcane, which must first be farmed in order to create PLA. Among the commonly used plastics, polystyrene is the worst; it is used for insulating so-called energy-efficient homes. It is also used for packaging fillers and the stabilizers used in the packaging of technical products. Its decomposition time ranges from 1,000 to 100,000 years. Are energy-efficient homes really that good?”
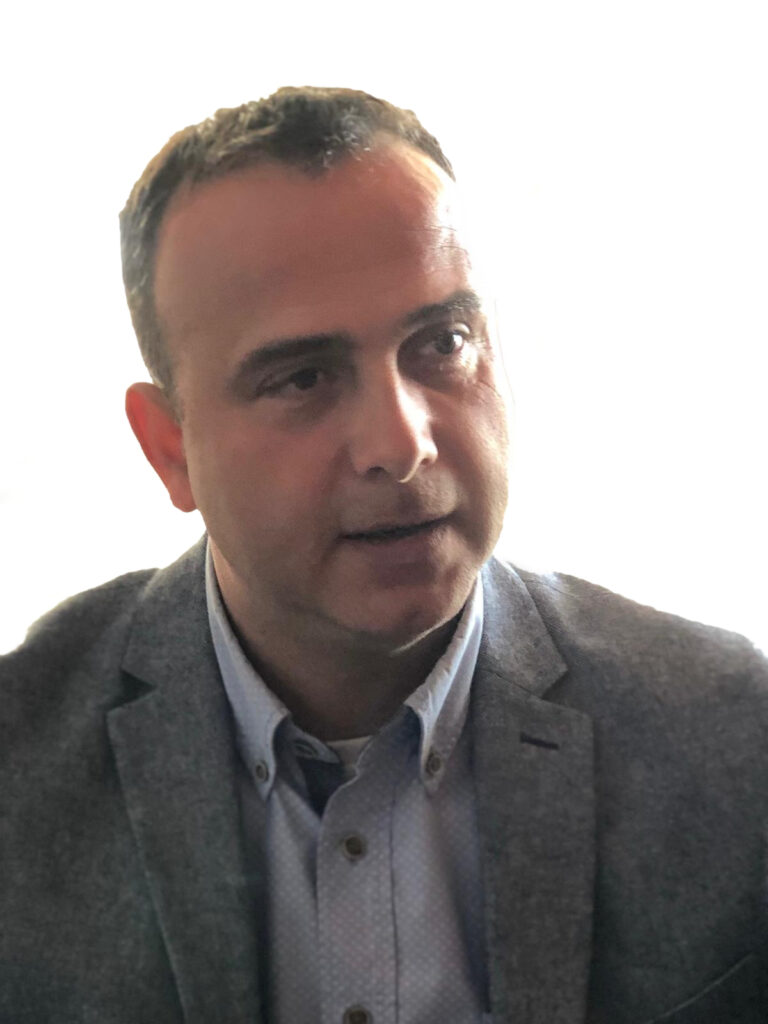
It is crucial to find the right balance between economic development and environmental considerations. Through our innovations and responsible decisions, we strive to ensure that the logistics industry serves not only businesses but also society and the environment. Here at INCON-LOGISTIC Ltd., we are prepared to meet challenges and are committed to continually searching for new, eco-friendly solutions. By taking responsibility for our future together, we can contribute to creating a greener and more sustainable world.
We extend our sincere gratitude to Viktor Rydzewski for sharing these insightful pieces of information with us.
You can access the CELLUX PACK Ltd. website by clicking here.