As the holidays approach, those working in logistics become true superheroes. Online sales are at their peak, and in offline retail, everyone expects fully stocked warehouses and shelves. The skills and precision of logistics professionals are crucial at this time to meet the expectations of both shoppers and retailers. But what factors contribute to the challenges? Below, we will help you understand the characteristics of the holiday season!
How does sales volume change during christmas?
According to the latest American data, retail sales typically show a 5-7% increase during the Christmas shopping season compared to the previous year. Incredible, isn’t it? Based on research from the National Retail Federation and similar studies, it can be stated that a significant portion of American retail sales, approximately 20-30%, is realized during the Christmas season. This highlights the importance of this period for the retail sector. Online shopping has changed our purchasing habits, and while it is becoming increasingly popular, offline shopping still plays an important role. Many people enjoy purchasing gifts in stores, savoring the festive atmosphere.
However, the extent of the increase may vary by region and industry. With the rise in online shopping, in addition to the increase in traditional store traffic, online sales also significantly contribute to the growth of global retail sales.
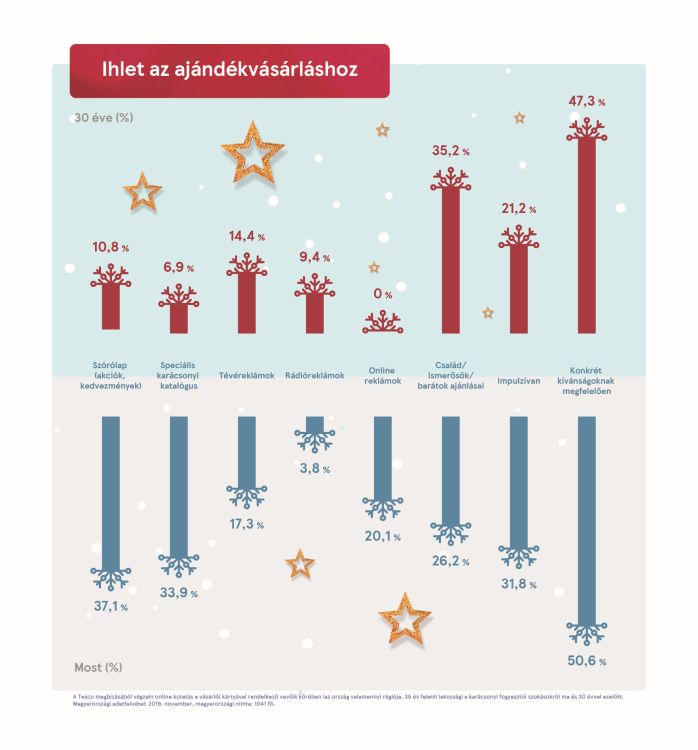
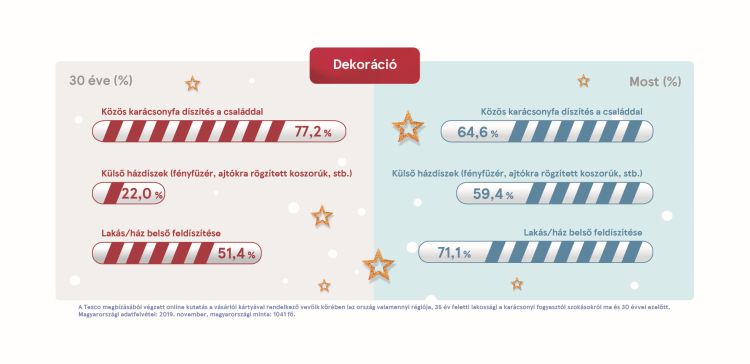
What to prepare for when shipping during christmas?
When we say that the burden on logistics chains dramatically increases during the Christmas season, it’s nothing new. A significant portion of the increased traffic is due to overconsumption, meaning the ordering and purchasing of products that are not necessary, or not necessarily needed during Christmas. More conscious consumption could not only reduce the burden on supply chains but also lower our ecological footprint.
The significant increase typically comes with meeting the heightened standards of warehouse capacity utilization and shipping periods. Logistics companies must be flexible during Christmas and develop strategies to manage the increased volume.
The most frustrating problem: Delays
Have you ever experienced late deliveries? Well, various factors are responsible for delayed deliveries, such as the high volume of orders, limitations on carrier capacity, or traffic congestion. Additionally, different external factors can influence supply chain disruptions, including weather conditions, labor shortages, or challenges in international trade.
A logistics company must proactively manage these issues, for example, by employing alternative transportation methods or expanding storage options. Beyond alternative methods, based on previous years’ experiences, logistics companies are increasingly monitoring trends related to the Christmas season to better prepare for anticipated challenges. According to existing data and reports, logistics companies often predict changes in the period leading up to Christmas and adjust their workflows accordingly.
HOW TO HANDLE CHALLENGES DURING CHRISTMAS?
In a previous article, we discussed the year-end rush, the multitude of tasks, and how to prepare for the upcoming year from a logistics perspective. The article includes 10+1 useful tips on how to smoothly start the next year and how to effectively plan logistics operations while considering various industry requirements.
Now, let’s take a look at how to manage challenges during Christmas!
- Always plan ahead!
– Adjust your shipping and warehousing schedules for the Christmas season to account for the increased demand!
– Check your inventory levels and start restocking your most sought-after products to minimize shortages. - Consider capacity expansion!
– If necessary, hire temporary staff for warehouses and transportation to manage the increased workload.
– Consider renting temporary warehouse space so you can work in parallel with your shipping processes. - Communication is key!
– Keep in touch with suppliers and communicate your expectations for the Christmas season so they can prepare accordingly! - Utilize technology!
– Look around and think about where you can incorporate technology into your processes to make things easier for yourself! - Be flexible!
– Stay updated on current news and global situations to make informed decisions!
– Be open to new options as well!
– If you get stuck, don’t hesitate to ask for help! - “What was it like last time?”
– Ask yourself this question!
– Try to create a brief feedback note for yourself regarding the holidays and any significant events (environmental factors or incidents) so that you can refer back to it, as past events often repeat themselves! - Set a goal and stick to it!
– Define what you want to achieve by the end of the year, be aware of the deadlines, and don’t let the Christmas rush hinder you in this! - Extra tips:
– Establish a priority system!
– Identify your most important tasks during this time and focus on those first.
– Do you already have a schedule in place?
STAY UP TO DATE!